When COVID-19 began tearing across the globe earlier this year, many businesses were forced—by regulation or conscience—to suspend operations and close their doors. Because manufacturers depend on healthy economic markets and a hands-on labor force, they were among the hardest hit.
With an end to the pandemic still many months away (if not much longer), communities and governments are eyeing sustainable ways to keep life moving forward. For many, this means finding a safe way to bring employees back to work.
“It is terrifying to shut down an assembly line. A company can lose tens of thousands [of dollars] in a single day,” says David Yanez, Founder and CEO of Andonix, as well as a manufacturing and safety expert. “Most companies cannot afford to shut down twice, so being able to stay open is a way to survive.”
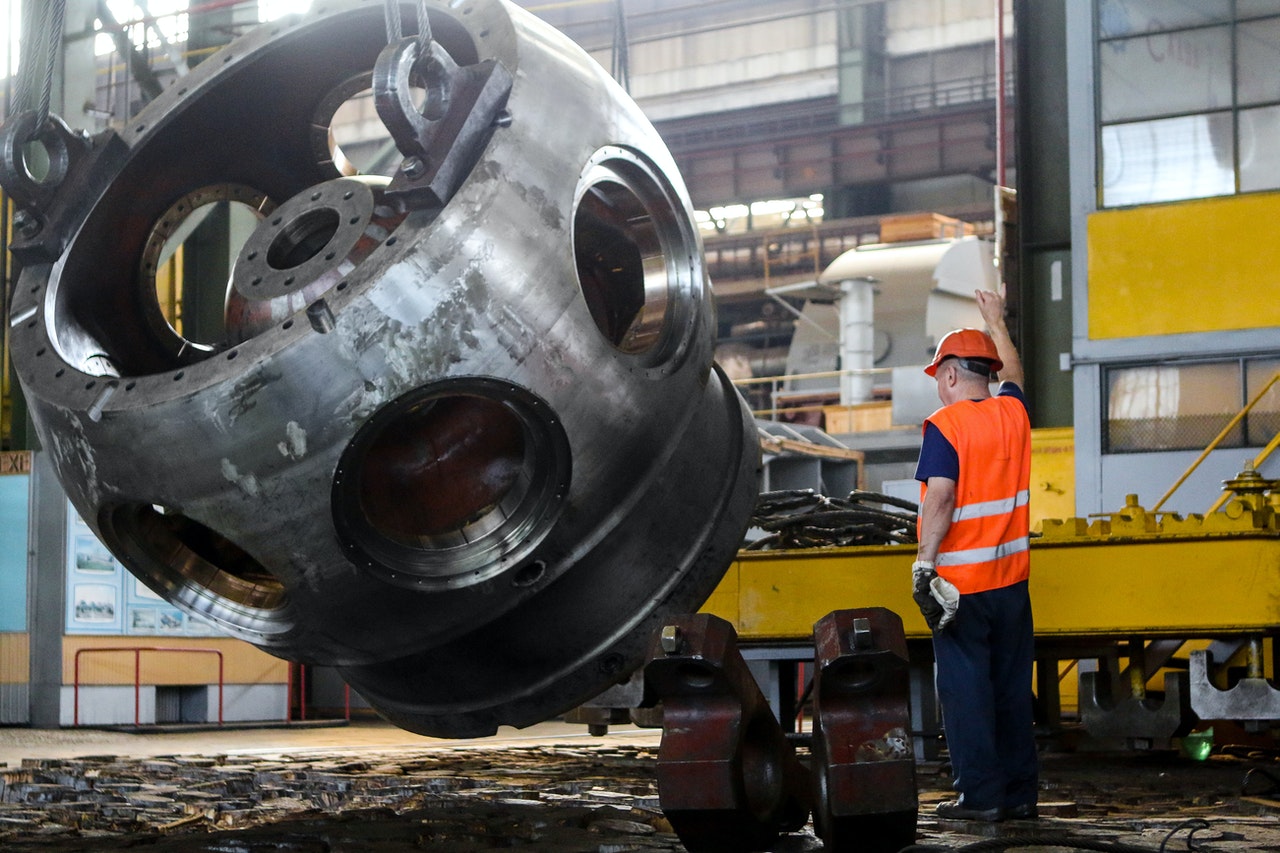
But how can businesses remain open with COVID-19 in the air?
A Comprehensive Workforce Health Strategy
In Yanez’s nearly two decades of working with manufacturers, he has watched the sector adapt successfully to trying times. He explains that while COVID-19 presents a unique challenge, it’s not an insurmountable one.
“When you get to the operating challenges for business continuity in the age of this novel health crisis, employers should be asking themselves, ‘How do I ensure people don’t become infected at work?’” he says. “For that, you need to have prevention, detection, and monitoring.”
As scientific knowledge about SARS-CoV-2 (the virus that causes COVID-19) has advanced, the Centers for Disease Control and Prevention (CDC) and the Occupational Safety and Health Administration (OSHA) have released resources that businesses can use to keep workers safe.
While useful, these have mostly focused on a number of now-familiar prevention guidelines, such as symptom checklists and recommendations for hand-washing, mask-wearing, and physical distancing.
However, these standard measures won’t be enough for many workplaces. Studies increasingly show that the potential for asymptomatic and pre-symptomatic transmission is real.
Thus, relying on symptoms to make decisions about who can safely come to work could mean missing a substantial number of cases. These concerns are only amplified by the very close-quarter working conditions typical in manufacturing.
“Factories are designed for efficiency, so operations and labor are happening in minimal square footage,” says Yanez. These close-quarter working conditions render the manufacturing sector particularly vulnerable to outbreaks—second only to the healthcare industry. “Suddenly, you have to reengineer assembly lines for social distancing. A lot of businesses want to follow guidelines, but it’s not always easy.”
Furthermore, Yanez notes, given the wide range of symptoms associated with COVID-19, dependence only on symptom reporting to identify potential cases could result in lengthy paid quarantines for individuals infected with a different, less dangerous, virus. This is where tests come in, explains Anders Boman, Founder and CEO of nationwide telemedicine platform Because Health.
“It’s difficult to screen and remove [infected] individuals unless you’re providing recurring testing,” says Boman.
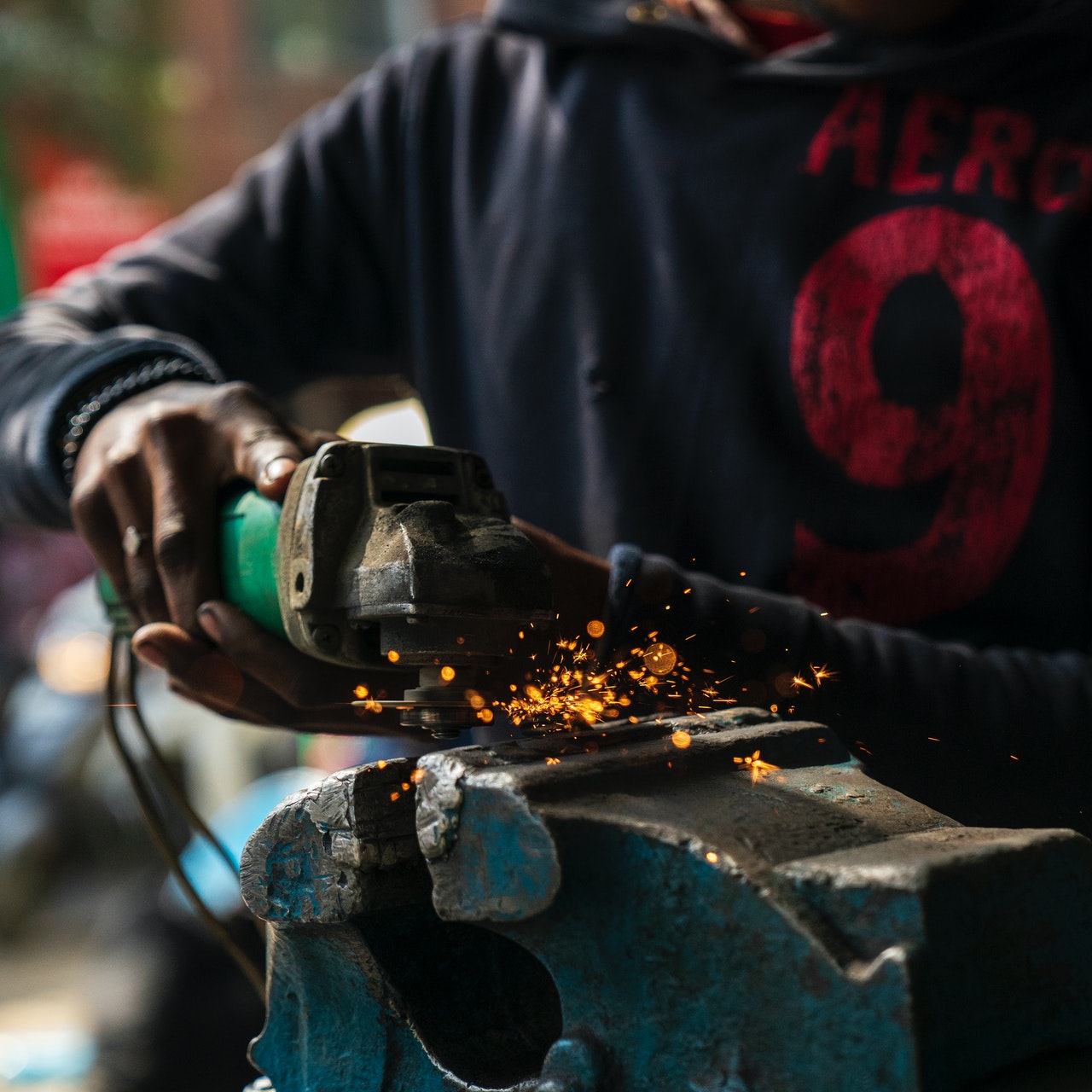
Indeed, the EEOC has recognized the importance of viral, or PCR, tests in the workplace. The organization recently stated that employers can require employees to get tested for the presence of SARS-CoV-2, the virus that causes COVID-19, as current infection puts other workers at risk.
Nonetheless, Yanez says, employers and employees alike face barriers when it comes to accessing usable test services.
Businesses that implement testing mandates without a plan in place may find that they are paying employees for lengthy travel to community test sites or time spent waiting in long drive-up lines. Another challenge associated with community testing, Boman says, is how long it can take to get results, especially in a location with high infection rates.
“The average turnaround time [for community test sites] is 7 to 10 days, and that’s way too long to have a containment strategy where you’re taking people out of work to prevent spread.”
That’s why Because Health launched its Workplace Health™ service. The program includes specialized risk monitoring, expert advising, and customized on-site testing strategies. The company uses only FDA-authorized tests and works with CLIA-certified laboratories able to offer an average turnaround of 24-hours. Healthcare experts work closely with each client to design a testing approach that makes sense for their particular needs.
“[We look at] what the community risk levels are,” explains Boman. “So, if the county has infection levels over a certain threshold, then we’ll recommend testing at a higher frequency; if it’s below that infection threshold, they may be able to test less often.”
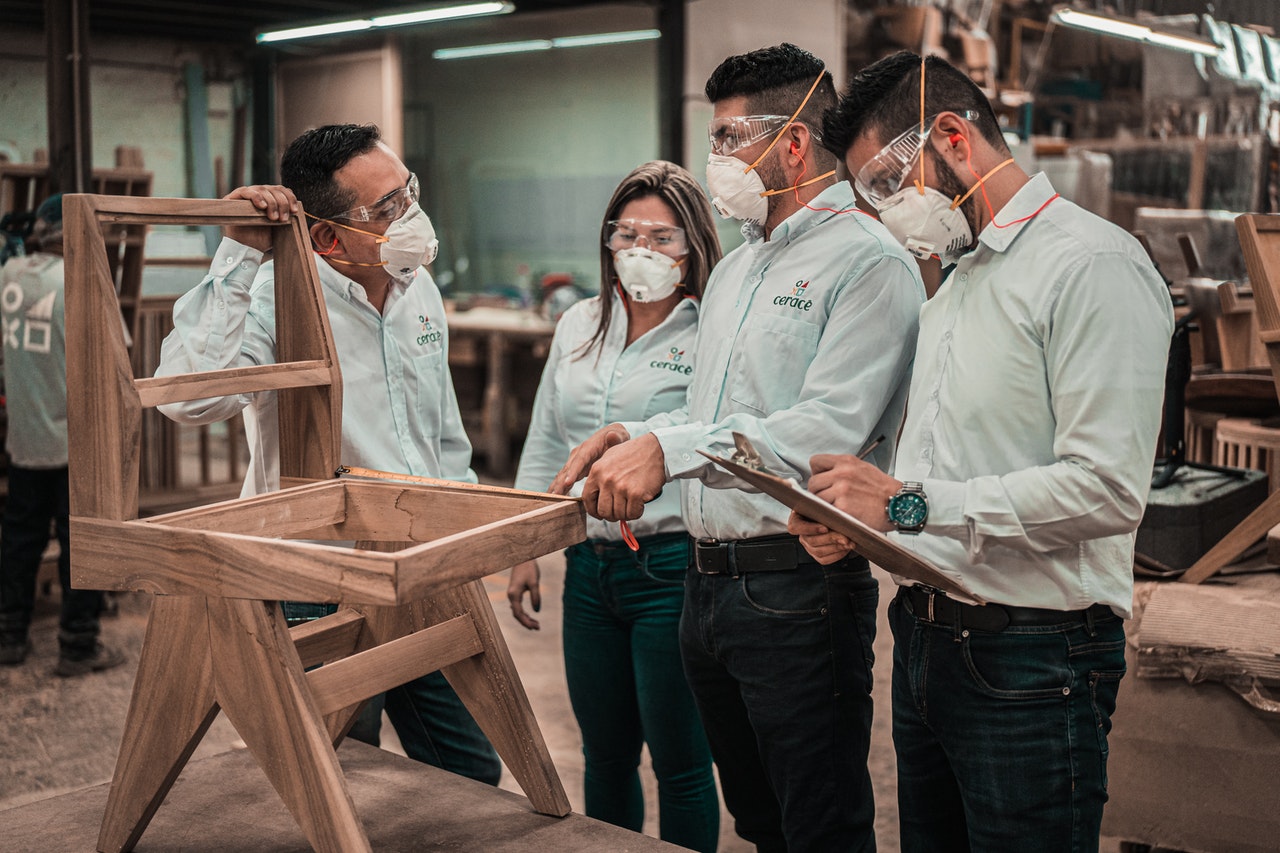
The standard plan focuses on PCR tests, since those indicate public health threat, but businesses looking to get a grasp on the bigger picture may also want to offer optional antibody tests. Such a robust testing strategy goes a long way toward mitigating risk of a workplace outbreak, providing workers with some well-deserved peace-of-mind. But, the Workplace Health program doesn’t stop there.
Anybody who tests positive will connect with a Because Health provider via telehealth before being referred to a community-based provider for further care as needed. Because Health’s experts work with employers to identify high-risk individuals and minimize exposure risk.
“We are doing a health risk assessment, looking at more than just who has signs or symptoms, but also what are their underlying health issues. If they’re at elevated risk of having worse symptoms of COVID-19, should they become infected, advisors can make recommendations about ways to adjust the workplace environment or alter shift schedules to keep those individuals safer."
Making all the changes necessary to minimize manufacturing employees’ workplace exposure to COVID-19 may be daunting or pricy to implement, Yanez says, but it's absolutely crucial to the health of your business and your workers. And with the right plan in place, that social responsibility will likely pay off in the long run.
Not only will compliant businesses be more likely to retain a workforce willing and able to do the job at hand, they will avoid the penalties, lawsuits, and shutdowns that result from outbreaks or violations.
“Compliance is costly, and 95% of manufacturers are small businesses.” However, Yanez stresses, “It’s the right thing to do.”